主讲老师: 欧阳光远(培训费:1.5-2万元/天)
工作背景:
欧阳老师,拥有25年的专注于生产领域的丰富研究经验。他对生产流程的深入了解以及对行业趋势的敏锐洞察力使他成为该领域的实践专家。上海坦达、美国百得电动工具、浙江野牛工具等多家企业在老师的辅导下实现了卓越的生产效率和质量提升...
主讲课程:
《质量问题解决之天龙八步(8D法)》《全面质量管理TQM》《现场改善与消除浪费》《现场问题分析与解决》《从检验员到质量经理进阶》《TPM设备全面生产维护与效率管...
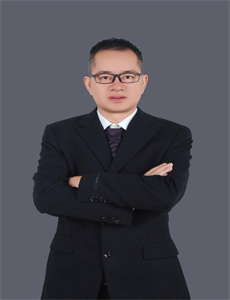
TPM设备全面生产维护与效率管理提升课程大纲详细内容
课程分类: TPM
课程目标:
1.帮助企业实现设备全面生产维护(TPM),提高设备利用率和寿命;
2.培掌握设备效率管理提升的方法和技巧;
3.推动企业实现生产现场优化,降低维护成本,提高生产效率
4.提升设备使用效率:减少设备故障率,提高设备利用率,提升生产效率
5.降低维护成本:降低设备的维护成本,包括人力、物力、财力等方面的投入
6.提高产品质量:减少产品缺陷率,提高产品质量,进而提高客户满意度
7.增加企业竞争力:提升企业的生产能力,降低成本,提高企业的竞争力
8.培养专业人才:培养专业的设备管理人才,提高企业人才素质
9.实现技术创新:可以了解并掌握最新的设备管理技术创新和方法
课程对象:制造业各职能部门经理、主管及生产部门、设备维护保养部门班组长级以上,及储备干部等生产运作相关的技术人员
课程时间:2天,6小时/天
课程破冰:学习型团队组建
第一讲:认识TPM
一、TPM的“全貌”
1.TPM的四大意义
1)减少设备停机时间
2)提高设备综合效率
3)提升产品质量
4)员工技能提升
2.TPM的六大重要性
1)保持竞争力
2)提升企业形象
3)优化资产管理
4)促进持续改进
5)增强员工参与和团队合作
6)降低维修成本
二、TPM的八个步骤与设备全生命周期管理
1.TPM的八个步骤
第一步:设备初期管理
第二步:制定设备保全计划
第三步:实施设备维护技能培训
第四步:进行自主维护
第五步:设定定期专业维护
第六步:精度检测与校准
第七步:问题反馈与改善
第八步:设备效率提升
2.设备全生命周期管理
1)设备引进评估:确保引进的设备能够满足企业的生产需求
2)设备使用管理:规范员工使用设备的行为
3)设备维护管理:定期的检查、保养、维修
4)设备报废管理:对设备进行报废处理
5)设备的循环利用:减少企业的生产成本
第二讲:TPM设备维护与保养与实践
一、设备预防性维护策略
设备故障分析:设备为什么会发生故障,设备故障对生产的影响
1.预测性维护
2.持续改进
3.配合生产线管理
4.与供应商合作
5.采用精益思想
6.建立应急预案
7.环保与安全
8.可追溯性管理
二、设备定期检查与保养计划制定
1.保养计划制定步骤
1)设备分析
2)制定保养计划
3)制定备品备件计划
4)实施保养计划
5)监控保养计划的执行情况
6)利用现代技术提高效率
2.保养计划中的五大注意事项
1)考虑设备的工作特点和运行状况,确定合理的保养周期和保养项目
2)根据设备的制造商和维护人员的建议,结合企业的实际情况,制定适合设备的保养计划
3)合理安排保养时间和保养人员,确保保养计划的顺利实施
4)在保养过程中,需要认真检查设备的运行状态,以及记录保养情况和处理潜在的问题
5)针对设备故障情况,及时采取措施进行维修和更换备品备件,以免影响生产
3.设备点检与巡检实施方法
设备点检的分类:日常点检、定期点检和专项点检三种
1)设备点检的方法:五感点检法、工具测量法、经验判断法:
设备巡检的分类:日常巡检、定期巡检和专项巡检三种
2)设备巡检的方法:定点巡检法、流动巡检法、自动监控法
工具:点检卡、听诊器检测仪器
软件工具:软件工具包括设备管理系统、数据分析软件等
案例:设备点检与巡检的案例
三、TPM活动与实践
1.自主维护与专业维护结合
1)划分责任区域
2)培训操作人员
3)制定自主维护计划
4)制定专业维护计划
5)协同配合
6)数据分析与改进
案例:某企业生产线自动化改造——从传统的手工加工模式到引入自动化生产设备和技术,对生产线进行全面改造
案例:某企业设备能源消耗降低——对设备的能源消耗进行详细的分析和研究
案例:某企业生产线信息集成与优化——原生产线信息孤岛现象,后建立生产管理信息系统
2.设备改造与优化的实施步骤和方法
1)问题分析:设备存在的问题和不足进行分析和研究,明确方向和目标
2)方案制定:制定详细的改造和优化方案,改进设备结构、优化运行参数
3)方案评审与修改:对制定的方案进行评审和修改,确保方案的科学性和可行性
4)方案实施:进行设备改造和优化,确保实施过程中的质量和安全
5)效果评估:包括生产效率、能耗、质量等方面的数据分析和对比,确认改造和优化的成果
6)总结与改进:总结和反思,及时进行改进和完善
案例:某制造企业的TPM推行
——推行过程:建立TPM推进小组+制定TPM计划+实施TPM活动+检查与改进
——推行成果:设备故障率降低+维护成本降低+生产效率提高
第三讲:TPM设备效率提升与管理团队建设
一、设备效率管理与提升方法
1.设备稼动率与综合效率分析
设备稼动率的计算公式:设备稼动率=实际作业时间/计划作业时间*100%
2.设备稼动率的分析与优化
3.综合效率分析的方法与步骤
1)确定分析目标:明确对象和目的
2)数据收集与整理:生产计划、实际产量、生产时间、人力、物力、能源等数据
3)计算效率指标:设备综合效率(OEE)、人均产量、生产周期等
4)原因分析:影响效率的因素和原因,设备故障、员工技能、生产排程等方面
5)制定改进措施:优化生产流程、加强员工培训、改进设备维护等
6)实施改进措施:实施进行跟踪和评估
4.减少设备停机时间策略
1)预防性维护与保养
2)快速更换易损件
3)设备故障预警与快速修复
4)优化生产计划与排程
5)采用先进的生产技术与工艺
实施减少设备停机时间的策略需要注意的问题:培训员工提高技能水平、建立完善的设备管理制度、持续改进与优化
5.提高设备性能与稳定性方法
1)选用高品质的设备零件
2)精细化设备维护与保养
3)正确操作与使用设备
4)引入先进的生产技术与管理模式
5)建立完善的故障诊断与预防体系
6)加强设备的预防性维护与保养
二、设备维护团队建设与管理
1.设备维护团队职责与分工
1)设备维护团队的五大职责
职责一:对设备进行日常巡检,及时发现潜在的故障和问题
职责二:对设备进行定期维护和保养,包括清洁、润滑、检查等
职责三:对设备进行预防性维护和保养,包括更换磨损件、调整参数等
职责四:对设备出现的故障进行诊断和抢修,尽快恢复生产
职责五:对设备性能进行评估,提出改进建议和方案
2)设备维护团队分工:电气工程师、机械工程师、维修工、技术支持工程师、培训师
3)设备维护团队建设与管理:选拔优秀人才、制定岗位职责、加强培训、实施绩效考核、加强沟通与协作、引入先进的维护管理方法和技术
2.跨部门协同与沟通机制
1)明确跨部门协同与沟通的重要性
2)设立设备管理专职负责人
3)建立跨部门协同与沟通机制
4)加强跨部门培训与交流
5)建立激励机制和评估体系
3.设备维护人员培训与成长规划
1)培训需求分析
2)制定培训计划
3)培训实施
4)培训效果评估
5)设备维护人员成长规划
——技能提升、职位晋升、职业发展、专业认证、建立奖励机制
6)持续反馈与改进
第四讲:信息化应用及安全/环境与健康
一、TPM信息化与智能化应用
1.TPM管理系统与软件应用
TPM管理系统的组成:设备管理、维护管理、备件管理、数据分析与优化等模块
TPM管理系统的软件应用:IBMMaximo、SAPMM
——TPM管理系统的发展趋势和未来展望
2.设备远程监控与故障预警
3.AI技术在设备维护中的应用与发展趋势
案例:某大型制造企业通过应用AI技术,实现了对生产线设备的实时监测和故障预警
案例:某电力行业企业应用AI技术,实现了对输电线路和设备的智能巡检
4.AI技术在设备维护中的优势和应用场景
优势:实时监测、故障预警、预测性维护、设备性能优化等优势
应用场景:生产线设备的实时监测和故障预警、设备智能巡检、设备性能监测与优化、智能维修管理等
5.AI技术的核心算法和模型
核心算法:深度学习、神经网络、自然语言处理、计算机视觉等
模型:神经网络模型、决策树模型、随机森林模型等
6.AI技术的未来发展趋势
——更加精准的故障预测与分类、更加智能的巡检与监测、更加自动化的维修管理
应用场景:人工智能技术在企业设备维护中的应排方案/步骤
数据收集和分析:温度、压力、振动、电流等参数
故障检测和预警:对比正常运行数据和实际运行数据,检测异常波动或趋势变化,进而触发故障预警
预测性维护:人工智能算法建立预测性维护模型,预测到故障时,提前准备好维修计划和备件库存
优化维修过程:制定合理的维修计划、安排专业的维修人员、提供及时的维修资源
培训和知识传递、持续改进和创新
二、环境、安全与健康(ESH)在设备维护中的关注点
1.环保意识与绿色维护策略(绿色维护策略的应用)
1)合理规划和设计设备
2)推广节能环保技术和方法
3)实施定期维护和保养
4)合理使用资源
5)推广再制造技术
6)关注员工健康和安全
案例:某企业在设备维护中采用绿色清洗剂
2.安全操作规程与应急预案制定
1)设备安全操作规程的制定
设备操作前安全要求:设备处于正常状态,工作区域内没有安全隐患,持证上岗
设备操作中的安全要求:严禁违章操作,保持现场整洁有序
——设备故障处理和紧急情况处理
2)应急预案的制定
事故或灾害类型的分析:确定可能造成的后果和影响范围
风险评估:确定可能的风险点及其应对措施
制定应对措施:包括人员组织、物资准备、通讯联络、现场处置等方面
应急物资准备:灭火器材、救援工具、应急食品、饮用水等
应急演练和培训:确保在紧急情况下能够迅速采取相应的应急措施
案例:某企业在生产过程中发生的一起火灾事故
——与时代发展紧密结合:关注最新的安全生产法规、标准和要求
3.职业健康与员工关怀措施
1)职业病危害因素的分类:化学因素、物理因素、生物因素等
2)职业病危害源的控制:通风、除尘、降噪
3)个人防护措施:防护服、手套、呼吸器
4)职业健康监护与培训
职业健康监护:定期的职业健康检查
职业健康培训:职业病防治法律法规、职业病危害因素识别与评价、个人防护措施等
5)员工关怀措施:心理健康+身体健康+工作环境+家庭关怀
案例:某企业在生产过程中存在一些职业病危害因素
第五讲:TPM推行
一、TPM推行八步法
第一步:制定TPM计划:目标、实施步骤、时间表、预算等
第二步:建立TPM小组:明确职责和任务,推动TPM计划的实施,协调各部门之间的合作
第三步:宣传和教育:认识TPM对提高设备效率、降低生产成本、提高产品质量的重要性
第四步:设备评估和分类:根据设备的重要性和风险程度进行分类
第五步:制定设备维护计划:维护的时间、人员、预算等
第六步:实施维护计划:清洁、润滑、检查、更换磨损件等
第七步:监控和维护效果:监控和维护效果的评估,及时调整和维护计划
第八步:持续改进
二、TPM成功的六大关键因素
因素一:领导层的支持和推动
因素二:员工的参与和培训
因素三:建立完善的TPM制度和流程
因素四:采用科学的方法和工具
因素五:建立良好的合作机制
因素六:持续改进和创新
企业实践案例深度剖析与经验总结:一家大型制造企业,拥有多条生产线和多种型号的设备然而,企业在设备维护和效率管理方面存在一些问题,如设备故障频繁、维护成本高、生产效率不稳定等为了解决这些问题,企业决定引入TPM全面生产维护与效率管理提升的理念和方法
分组讨论:学员互动与问题解答环节