主讲老师: 许忠宁(培训费:1.5-2万元/天)
工作背景:
著名生产管理咨询师、培训师精益生产管理与班组长管理专家上海复旦大学MBA,黑带大师广东省多家知名咨询公司技术总监拥有10年以上日资企业高层管理经验15年实战工作经验+10年咨询与培...
主讲课程:
《精益生产》、《生产计划与物料控制》、《卓越现场管理》、《金牌班组管理提升》、《目视化管理》、《SOP标准作业流程》、《设备TPM管理与OEE提升列》、《VSM价值流分析与工厂精益改善》、《中国企业供...
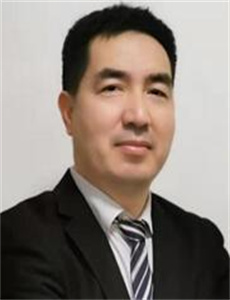
精益生产整体方案课程大纲详细内容
课程分类: 精益生产
课程目标:
相对系统掌握精益的概貌和工具
掌握现场改善的逻辑和问题解决的结构化方法
被培训者对问题的重新认识和深刻理解
收获突破性的思维训练
现场管理者综合管理实战能力得到提升
课程对象:生产部长、车间主任,现场班组长等现场管理者
课程时间:6天
第一课:精益生产管理之现场6S管理
一、正确认识6S
1.破冰:大家谈6S推行中的现存问题及困惑
2.情景回顾,状况呈现
3.何谓6S活动
4.6S的起源、含义及其发展过程
5.为何要导入6S
6.6S是改善的基础
7.6S的推动顺序
三、6S推进的误区
1.6S推行很简单
2.工作太忙,没有时间做6S
3.6S细节及标准化管理会束缚员工的创造性思维
4.6S活动就是检查
5.公司已经做过6S了
6.6S活动就是大扫除
清扫与产品品质
清扫与设备管理
案例:机器设备的清扫点检
4.清洁推进重点及案例
清洁推进的重点及步骤
做不好清洁所导致的问题
标准化建立
如何建立6S检查体系
清洁工作的延伸
案例讨论:规章制度为何难以执行
5.素养推进重点及案例
素养推进的重点及步骤
素养提升的三大方向:知识、技能、态度
6S源于素养,终于素养
提高员工素养的几点作法
6.安全推进的重点及案例
安全推进的重点及步骤
企业不安全现状和不安全行为大扫描
做不到安全所导致的问题
安全管理“六到”原则
案例:现场安全隐患分析
五、6S推进的实务手法及案例
1.日本工业企业的五现手法
2.定置管理法推广及实施案例
3.目视、看板及颜色管理法推广
4.红牌作战及流动红旗
5.5W1H思维方法及PDCA法
6.实景拍照及摄像前后对比法
7.案例:某纸业公司(设备生产型)
6S推进方法详解
二、6S内容及理解
1.整理——清理杂乱
提示语:快刀斩乱麻
整理的含义及目的
2.整顿——定位管理
提示语:简单最好
整顿的含义及目的
3.清扫——清除污尘
古语:一屋不扫,何以扫天下
清扫的含义及目的
4.清洁——保持乾净
古语:无有规矩不成方圆
清洁的含义及目的
5.素养——养成习惯
古语:十年树木,百年树人
素养的含义及目的
6.安全——如何保护全员安全
提示语:安全责任重于泰山
安全的含义及目的
四、6S推进重点及案例
1.整理推进的重点及案例
整理推进的重点及步骤
做不好整理所导致的问题
空间是怎样让出来的
区分必需品和非必需品的实用方法
处理非必需品的方法
案例:某重型机械车间工具柜及货架整理推进
2.整顿推进的重点及案例
整顿推进的重点及步骤
整顿关键活动:分类、定位、标示、归位
整顿实施方法
案例:车间模治具及现场文件整顿案例
3.清扫推进重点及案例
清扫推进的重点及步骤
做不好清扫所导致的问题
如何杜绝污染源
六、6S巡查与检讨
1.没有检查就没有执行力
2.6S巡查的标准制定
3.6S巡查小组的建立及要求
4.巡查结果公开及透明化
5.如何将6S考核纳入绩效管理当中
6.问题改善和跟进
7.如何强化一线干部的问题意识
8.如何培养员工的改进意识及危机意识
9.如何提升员工的执行能力
10.6S成果发表会
11.案例分享:某台资企业6S评分方法详解
课程总结及课后作业布置
第二课:精益生产管理之现场安全管理
一、安全是什么
1.安全—指判明的危险性不超过允许的限度
2.使人不受伤害和危害的影响
3.没有危险或灾难的威胁
4.不受财产损失的威胁的状况
5.没有危险,不产生伤害的一种状态
二、安全为了谁
1.安全是为了社会的稳定。
2.为了企业的发展
3.为了职工的健康,
4.为了家庭的幸福安宁
三、为什么要进行安全培训
1.对员工进行安全教育是国家法律法规的要求
2.对员工进行安全教育是企业生存发展的需求
3.对员工进行安全教育是员工自我保护的需要
四、安全生产的目的
1.不伤害自己
2.不伤害他人
3.不被他人伤害
4.保证他人不被伤害
五、事故的四种形态
1.不安全状态
2.不安全行为
3.未遂事件
4.事故
六、安全事故链
1.危险
2.事件
3.事故
4.事故发生流程图
5.海因里奇法则
6.墨菲定律
7.安全控制点
七、安全KYT分析
1.KYT定义
2.KYT基本方法
3.LEC值定义
4.安全危险源的识别与改善
5.危险预知训练
第三课:精益生产之价值流分析
一、精益生产起源及其本质
企业为什么推精益生产
精益核心思想
精益的起源
精益生产方式的产生
精益的基本架构和内容
精益的五项基本原则
精益生产对企业的重要意义
精益生产实施过程全貌
二、精益生产的目的:消除七大浪费
什么浪费(MUDE)
精益生产中Muda观念
什么是价值
如何寻找企业增值与非增值工作
生产过程的七大浪费工序本身的浪费
不良品的浪费
搬运的浪费
库存的浪费
制造过度的浪费
动作的浪费
等待的浪费
练习:讨论我们企业生产过程中存在的主要浪费
三、精益生产实施:价值流
1)什么是价值
2)精益价值流简介
3)企业价值分析的方法价值流图
4)制作价值流图的四大要素
5)练习:制作企业价值流图
6)如何设计未来价值流图的准则
7)设计未来价值流图的关键问题
8)如何绘制企业未来价值流图
9)改善价值流中的关键环节
10)练习:制作未来价值流图
四、防错技术
防错技术等式
检验技术和零缺陷三个级别
防错技术的核心思想
防错十大原理(案例分享)
五、看板管理与拉动式生产
物料运动和拉动系统
拉动系统:看板之种类
拉动系统:看板如何工作
拉动系统:支持流动
拉动系统:工序看板与计算
拉动系统介绍:单点节拍控制-均衡生产:品种、顺序、批量
第四课:精益生产之设备TPM管理
第一章:了解全员设备管理TPM
一、TPM发展历程
1.TPM前身的五阶段
BM事后保全
CM改良保全
PM预防保全
MP保全预防
PM生产保全
2.TPM扩充的三层次
TPM
生产保全
预防保全
3.TPM当前的新系统
企业人机系统精细化管理体系
全员参与的现场自主维护体系
全系统生产维护维修体制
二、TPM定义理解
1.TPM定义一览表
2.TPM定义的特点
全效率
全系统
全员工
3.TPM定义的内涵
三、TPM内容要求
1.三个方面的内容
设备管理
预防性及预见性维修
自主维护
2.两种关键人员
操作人员——一线“医生”
维护人员——专业“医生”
3.三降一提目标
四、思考填空:TPM全员参与指的是?
五、案例:某企业TPM管理成功案例说明
第二章:强化设备专业保全基础
一、设备专业保全总的要求
1.分工与合作
2.保全的方式
3.方案的例子
二、构建预防系统
1.把握设备现状
2.劣化弱点改善
3.强化信息管理
4.策划定期保全
5.制定预知保全
6.计划保全评价
7.案例分析:某企业预防保全制度
三、及时维修
1.及时维修框架:流程设备管理总体框架
2.故障树维修术:故障树分析实例
3.现场讨论:设备运行当中出现了停机,
维修人员应在多少时间修好?
4.维修的限时性:最佳状态的思考方法
5.同故障重现性:设备零故障的五项对策
6.备件计划管理
备件ABC管理
备件标准化
费用问题
案例分析:某企业备品备件管理办法
第三章:开展全员设备自主管理
一、明确要求
1.运转保全两轮
2.设备人员素质
三好
四会
五纪律
3.自主维护三项
设备日常保养
设备日常点检
案例分析:某企业日常点检表范例
设备的巡检
互动讨论一:5S管理当中的清扫、清
洁与TPM有哪些关系?
二、六步构建
1.始于清扫点检
清扫不彻底会引起的弊害
清扫的要点
2.困难部位改善
切断污物发生源
使清扫点检更加容易
3.制定保养基准
图示:某企业自主保养执行基准书
4.形成总点检表
总点检表必须要做好
点检项目选定程序
5.指导自主点检
6.标准化之建设
三、全员落实
1.首先做好6S
2.密切追踪6H
3.灵活应用6I
4.天天实施6T
5.用心追求6Z
6.互动讨论二:现场人员在自主保全中
会出现哪些“形式主义”,例如提前勾
选点检记录等,出现了“形式主义”该如何处理?
第五课:问题发现与系统性改善
一、如何发现问题
什么是问题.
面对问题的心态
·问题的四种发生类型
·认识和识别问题的根本原因·
问题分析与解决正确之程序.
二、问题分析与解决技巧
·问题基本分析工具
两图一表工具的应用
·找出主要原因的方法
·案例:你会如何处理这件事?
三、现场问题解决的系统思维方法·
问题5Y分析手法应用
·问题处理四步法
·从游戏中体会解决问题的方法
四、目标设定的SMART原则
能力范围的
可测量的
有吸引力的
切合实际的
有时间限制的
五、原因分析
分析问题的真实含意
问题分析时的逻辑
如何找出问题的原因
如何界定核心原因
分析问题常用的技巧与工具
因果图的使用技巧
演练:因果图
六、解决方案
1.解决方案的标准
2.开发解决方案的工具
3.头脑风暴的四大原则
4.演练:头脑风暴法
5.第一标准的审议与确定
6.对策候选单的建立
7.评估对策的工具
8.决策矩阵使用技巧
9.演练:决策矩阵
七、工作改善与心态的关系
改善的误区
工作改善从哪入手
如何让改善持续下去
展开新方法作法学员发表提案
工作改善\工作成本与工作效率.
改善方法领悟
改善合理化的四个步骤
把有效的改善模式,运用于工作中.
改善的八字诀
八、帮助员工拥抱变革
改善带来的影响
工作改善与心态的关系
改善的误区
工作改善从哪入手
如何让改善持续下去
·展开新方法作法学员发表提案
工作改善\工作成本与工作效率