主讲老师: 陆伟华(培训费:1.5-2万元/天)
工作背景:
主讲课程:
《精益生产管理实战培训》《金牌班组长》《现场管理实务》《运营成本管控》《卓越绩效体系建立》
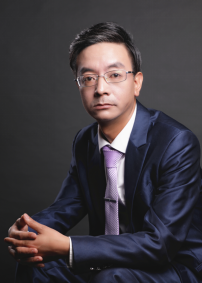
中国式精益生产落地实践课程大纲详细内容
课程分类: 精益生产
课程目标:
系统了解精益生产管理方式与传统生产方式的区别,寻找现场改善之突破口
熟练掌握现场管理的五大要素,全面出击,确保高效地实现现场的六大目标
从现场的七大浪费切入,从根本上诊治与根除现场浪费,提升效益
通过节拍管理与快速换型,满足多品种小批量生产
通过二大原则与十大技巧,掌握紧急订单与插单处理方法
通过现场标准化管理,制定标准工时与均衡生产,达到生产均衡高效
通过TPM方式的设备管理,让你的设备稳定高效
熟悉现场改善IE七大手法,结合案例分析,确保做到学后即用
课程对象:生产副总、生产总监、生产经理、生产主管、班组长
课程时间:2天,6小时/天
前言:理解中国企业
1.中国的文化是什么
2.中国的企业管理现状及人员能力
3.为什么中国100年品牌并不多
4.想厉害了我的国,出路在哪里
第一讲:认识精益生产管理
1.何为中国式精益生产管理
2.精益管理意识之养成
3.找准改善的突破口
4.实现精益生产的六个目标
1)如何提升效率
2)如何提升产品质量
3)如何降低生产成本
4)如何保障生产安全
5)如何提升员工士气
6)如何确保交期
5.实施方案的构建
6.生产改善工具
7.如何破解改善阻碍
8.灵活运用精益化管理
9.成功辅导企业精益化管理亮点分析
案例分析:对企业改善的认识分析
视频:丰田制造系统
研讨:什么是中国式精益,该如何做
第二讲:精益生产二大支柱之——5S管理(或XS)
1.5S实施要领与作业技巧
2.5S实施之21种工具
3.生产现场全面目视管理
1)安全目视化
2)交期目视化
3)品质目视化
4)产值目视化
4.5S推行不成功原因分析与对策
5.提案改善实施办法
6.企业推行提案改善几点现实建议
1)创新奖励机制的建立
2)创新等级的划分
3)创新团队的建立
4)创新成果的发布
5)创新大赛的举办
案例:《5S区域责任划分张瑞敏说法》
实操演练拿现场一处做5S演练
案例分享:车间现场改善前后5S照片
讨论:如何在公司推行5S
分享:《标准化手册》
第三讲:精益生产二大支柱之——消除浪费
1.企业过量生产控制方法
2.过量库存的控制方法
3.如何控制搬运浪费
4.不良品浪费的控制途径
5.过程加工控制方法
6.如何减少等待浪费
7.动作的控制方法
8.系统分析与改善——结构决定功能
9.如何减少库存
10.搬运路线及工具的合理化设计
11.如何实现人、机、物合一
小组讨论:举出本公司三大浪费及提出对策
讨论:为何说推诿是等待的另外一种方式,领导认可是不负责任的表现
第四讲:用均衡化实现生产稳定
1.生产计划坚持原则与注意事项
2.应对急单插单的策略
3.生产线平衡改善原则
4.TVAL模型量化作业负荷
5.标准工时管理和工序分割实现均衡
6.设定标准时间的三种方法
1)专家评估法
2)秒表测试发
3)综合评定法
7.产线均衡率计算与案例分析
范例:《标准工时测试记录表》《生产排线图》《换线作业指导书》
练习:计算改善前后产线均衡率各为多少
第五讲:全员生产保全之TPM
1.如何采购合适的设备
2.自主保全确保设备正常运转
3.专业保全确保设备零故障
4.个别改善鼓励全员参与
5.人才育成培养专家型员工
6.SMED快速换型的原则
7.如何实现SMED快速换型
8.SMED改善实施步骤
案例分析:丰田设备自主保养必做的三件事
练习:《设备点检指导》找错练习
案例分享:美的电磁炉公司TPM实施经验分享
表格:《班组安全运行表》《不合理表》《异常记录清单》《设备故障时间管理推移图》《设备运行不合理表》
第六讲:IE七大手法改善作业
1.IE改善遵循的原则
2.防呆法防错
3.动改法四原则
1)剔除
2)优化
3)合并
4)重排
4.如何看透问题找到良策
5.优化流程提升效益
6.减少动作的浪费使作业轻松高效
7.作业过程高效监管
8.人机法人机合一协调高效
范例:《动改法操作表单》《流程优化操作表单》
讨论:我们在生产过程中有哪些可优化的,如果优化完成后能提升多少业绩
第七讲:用TQM快速实现产品质量提升
1.质量意识提升
2.质量问题预防及解决
3.首件管理与过程控制
4.8D将问题解决到底
5.总体分析让质量综合成本最低
6.QC小组活动与全员质量管理
案例分析:违禁物超标导致的沉痛教训
互动:说说让你痛心的质量事故经历与体会
互动:指出此改善报告都有那些问题
讨论:我们的质量问题有哪些,痛点是什么,如何解决
第八讲:精益项目的推进
确定推进的范围
1、建立推进组织
2、确定推进方案
3、制定推进计划
4、奖励优秀团队
5、继续PDCA
6、研讨:我们该如何组织我们的改善组织
我们如何推进我们的精益改善