主讲老师: 李丰杰(培训费:1.5-2万元/天)
工作背景:
清华大学工商管理硕士(MBA)工商管理博士(DBA)华夏精益研究院院长日本丰田出身的精益研修员工信部第五研究所特聘专家华中科技大学、上海交通大学、厦门大学客座教授中国管理科学院经济发展研究中心智慧...
主讲课程:
《现代制造业职业经理人“三力管理”模型构建》《数智化环境下的生产运营管理模式变革》《国有企业“三精管理”》《精益生产运营管理实战系列课程》《全员成本管理——TCD》《全员设备管理—...
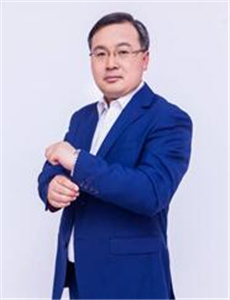
精益生产运营管理系统培训解决方案课程大纲详细内容
课程分类: 精益生产
课程目标:
全球视野拓展制造业经营思路,了解经济发展最新资讯;
在经济下滑的环境下,认识企业从内部管理如何的转变;
掌握市场营销新思维,为市场营销“插上翅膀”;
掌握ERP/MES/MRP/WMS/PLC等多种工具在工厂运营实战中的运用;
从信息流和实物流的角度来分析“企业烧钱”的运营模式;
从精益运营的角度系统分析价值流程;
如何从采购、仓储、研发,生产、技术等环节分析价值点;
熟练掌握工厂运营过程中改善管理问题的工具;
如何在生产场景识别生产现场的八大浪费,通过案例分析展示精益生产各种工具和方法;
用能理解、记得住、用的上的方式,熟练掌握数字化、智能化和精益运营结合的复杂理论。
课程对象:制造业中、高管理人员
课程时间:4天,6小时/天(
第一篇:全面打造精益运营企业
第一讲:我们处在变革的时代(历史迫使我们转变)
1. 中国企业改革40年GDP回顾及展望
2. 中国近期经济政策解读
3. 中. 德. 日. 美工业管理特点
4. 中国企业的困难点及转折点
5. 企业内部生态圈准时化搭建势在必行
6. 精益企业构建三大运营核心
第二讲:制造业运营精益化
一、现代化运营管理模式
1. 精益思想与数字化. 智能化时代结合
2. 运营管理由效率转换成效能
3. 运营管理由管理转变成经营
视频:目视化精益工厂理想状态
4. 微笑曲线与武藏曲线
5. 什么样的企业实施精益管理效果最佳
二、营销价值链分析(案例)
1. 创新模式市场营销
2. 品牌模式营销
3. 垄断模式营销
4. 差异化营销管理
工具:数字化营销模型
三、研发、技术、工艺价值链分析及对生产系统的影响
1. 研发与生产成本之间的关系
2. 技术成本与生产现场的关系
3. 工艺严谨性对生产效率和质量之间的逻辑关系
4. 智能化时代研发、技术新突破点
案例:国内三个大型企业的技术FEMA展示
互动游戏:魔术般的红心
四、从运营角度看财务价值链分析
1. 正确解读资产负债表
2. 正确解读现金流量表
3. 正确解读利润表
4. 资金流转速度和投入量对运营的影响
案例:一个财务人员顶千军万马
案例:某大型企业财务报表解读
第三讲:制造业内部供应链精益化
一、内部供应链价值分析
1. 管理好“入口——采购与原料仓储
2. 调整好“胃口”——生产内部供应链
3. 管理好“出口”——成品库与客户供应链
互动:人的身体与内部运营各部门的关系
二、价值流程分析(VSM)
1. 价值流程分析的原理
2. 价值流程分析的结论
3. 信息流与实物流的误解
1)信息流的浪费才是最大的浪费
2)整理信息流与实物流
案例:一个20天交期如何缩短40%
4. 如何做价值流程图
案例:中车集团价值流程分析过程
三、采购与仓储价值链
1. 采购成本分析图
2. 供应商评价策略与谈判
3. 采购体系搭建
案例:采购管理ERP智能化建设
4. 原材料储存ABC与采购策略调整
5. 标准库存量的计算与考核
6. 仓储部门三不原则
7. 仓储账、物、卡之间的关系
8. 成品库治理实战
案例:仓储管理ERP智能化建设
第四讲:生产现场精益化
一、改善从识别和消除浪费开始
1. 生产现场八大浪费现象
思考:生产现场浪费如何形成的?有什么危害?
2. 生产浪费现象治理的分类
二、精益准时化物流控制搭建
1. 拉动式计划与推动式计划(TPS互动)
2. 生产能力均衡化(TOC理论)
3. 生产计划的“前生和后世”(PMC互动)
1)生产计划在整个运营系统的地位与作用
2)生产MES系统推进的组织改善
3)生产调度、生产物流、生产管理的关系与分工
案例:MES系统模拟排产
4. 单件流的计划与实施
案例分析:如何做拉动式计划
三、精益生产人、机、料、法、环、信息的管控
1. 日本丰田的自働化蕴含着人的秘密
2. 设备TPM中的OEE是衡量生产效率的最佳指标
3. 物流及时化是保证生产效率的根本
4. 现场6S管理是生产环境治理的最佳方法(全图式讲解)
5. 生产方法的调整策略
1)应对小批量、多品种的技术——SMED
2)质量保证——标准化建设——TQM
3)人机互动最佳手段——IE工程学
4)丰田问题改善八步法是生产改善最全的工具
5. 信息流建设
导入:智能化工厂的特点
——纵向集成化工厂、端对端集成工厂、横向集成工厂
分析:智能工厂的未来发展四大趋势
四、精益运营推行实战
1. 推行精益运营五忌
2. 推行精益生产运营的要点与难点
3. 成功推行精益生产运营五步骤
第二篇:全面打造精益生产现场企业
引言部分:精益生产管理意识的转变
一、精益生产概论
1. 精益生产起源与原理
2. 精益、精细、精准三大概念实施场景
思考:为什么要做精益生产
工具:精益生产五大指导原则、丰田4P模型
3. 生产成本与利润的关系
4. 无缝管理与管理流程
5. 精益之屋解读
第一讲:生产现场精益先从浪费识别开始
一、生产现场八大浪费现象(如何形成的?有什么危害?)
1. (Waiting)等待的浪费
——等待:上级指令、外部回复、下级回复、生产联系
2. (Over-production)过量生产的浪费
——造成原因:工作进度不协调、信息传递不顺畅、生产计划做不到有效贯彻执行
3. (Inventory)库存闲置的浪费
——库存的浪费(原材料、生产过程、成品库存)、工序复杂的浪费、职能闲置的浪费、信息流的节流闲置浪费
4. (Correction)不良作业及无序浪费
——质量控制不到位的浪费、不遵守流程作业的浪费
5. (Conveyance)搬运及失职的浪费
——多余动作的浪费、工作任务完成不到位的浪费、布局不合理的浪费、虎头蛇尾的浪费
6. (Mistake)失误及低效的浪费
——工作无质量浪费
7. 动作的浪费
——现场布局不合理、十二种典型的动作浪费现象
8. 管理成本的浪费
——计划编制无依据混乱、计划不执行、计划处置不当、成本意识不强
总结:生产现场八大浪费现象归类——现场人、机、料、法、环、信息
第二讲:精益生产现场人员管理
一、开启生产员工心理密码
1. 不同类型员工的心理状态
2. 如何利用不同员工特点开展工作
3. 前喻时代员工的特点及管理方法(60-70年代)
4. 并喻时代员工的特点及管理方法(80-90年代)
5. 后喻时代员工的特点及管理方法(00后年代)
1)兼有积极和消极的工作态度
2)多变的职业观点
3)对成功的独到界定
4)对权威的看法
5)信息化的优势
6)不太喜欢循规蹈矩
7)忠于自己的生活方式,而不是自己的工作
二、解开沟通密码
1. 现场管理沟通密码
2. 如何和不同类型的上级有效沟通
3. 如何和平级沟通
4. 如何和你下属沟通
互动:现场分析不同性格的处事规则,解读协密码
第三讲:精益现场效率提升
一、生产计划的编排
1. 同期化思考与生产计划编排
2. 生产节拍的控制
3. 生产周计划. 月计划. 日计划的编排
4. 生产计划甘特图的制作
案例:某公司的生产计划
二、现场准时化生产技术的运用
1. 现代流水线的布置
2. 生产物流的控制关键点
3. JIT技术的运用
4. 单件流技术的实施要领
三、现场快速切换技术的运用
1. 应对“多品种. 小批量”订单的秘诀
2. 快速切换技术的技术要领
3. 快速切换技术实施步骤
案例互动:一顿完美的早餐
四、现场TOC技术的运用
1. 木桶原理新解读
2. TOC技术介绍
3. TOC技术的实施要领
案例互动:爸爸的红茶
第四讲:精益生产现场环境管理(6S活动)(案例图片分析其的步骤与要领)
1. 整理
2. 整顿
3. 清扫
4. 清洁
5. 素养
6. 安全
案例分析:6S目标化推行与落实. 关键要素列举
第五讲:精益生产现场质量管理
一、质量意识的改变
1. 什么是质量
2. 质量成本有哪些
3. 品质问题没有折扣
4. 精益生产解决质量问题的办法
案例分析:海尔的质量意识
二、现场分析质量问题的方法
1. 头脑风暴法
2. 5W法
3. 4M1E法
4. 如何写质量分析报告
案例互动:如何灵活能运用所学方法做质量分析
三、质量问题的处理方法
1. 戴明的PDCA循环
2. 过程作业模式技巧
3. 生产操作标准写作技巧
4. QCC活动的实施方法
案例分析:某国内大型企业的QCC活动
四、标准化作业指导部下四步法(不完善的指导方法演练)(一个视频场景)
1. 正确的指导方法演练
方法:工作指导4阶段法
——让对方准备学习、说明作业、让对方做做看、看看教导之后?
2. 正确运用阶段法的4项准备工作
——订立训练计划、分解作业(作业分解的讲解-标准案例)、准备全部的东西、整理作业场
案例互动:提高员工实际操作技能的指导要点?
第六讲:精益生产现场设备管理
一、认识设备管理
1. 设备管理在生产管理中的地位
2. 设备管理中的十大浪费
3. 设备管理的衡量指标
4. 案例分析设备的衡量指标—OEE
二、开展自主保养活动
1. 如何理解自主保养
2. 班组长如何实施自主保养
3. 企业实践自主保全活动7步骤
Step1:初期清扫
Step2:污染源及困难处所对策
Step3:制定自主保养临时基准书
Step4:总点检
Step5:自主点检
Step6:工程品质标准化
Step7:彻底的自主管理
4. 成功推行自主保全的要点
演练:TPM自主保全活动计划书及活动要点讨论
三、TPM计划保全活动实务展开
1. 计划保全的基本观念体系
2. 如何正确处理计划保全与自主保全的关联
3. 设备日常维修履历管理
4. 实践设备零故障的7个步骤
Step1:使用条件差异分析
Step2:问题点对策
Step3:制定计划保养临时基准书
Step4:自然劣化对策
Step5:点检效率化
Step6:M-Q关联分析
Step7:点检预知化
分享:TPM活动企业成功案例
演练:TPM计划保全活动计划书及活动要点讨论
第七讲:精益生产现场改善常用方法(实施借鉴)
方法1:“头脑风暴法”
方法2:“特性要因理论”
方法3:“4M1E理论”
方法4:“柏拉图分析”
方法5:“对赌行为”(解决执行力问题实施诀窍)
案例分析:某大型企业现场质量改善各种工具灵活运用